Our Second back2basics
In our last issue of back2basics, we reviewed the technology of pearlescent pigments. That subject matter had more to do with the science of optics than the science of chemistry. This article continues with that science to help explain how metallic pigments of aluminum and brass (silver and gold as we call it in the industry) create the effects we see. We are proud to represent Eckart America for their line of "effect pigments" including aluminum, brass, and pearl which are widely used in coatings, plastics, and graphic arts.
It is our hope and objective that you will find this and future issues of back2basics sufficiently informative and technically in-depth to save to your electronic library. A PDF format is available by e-mailing us at info@spmorell.com.
Metallic Pigments – The Science of Optics
Aluminum Powder Production
Aluminum itself is reflective and corrosion resistant. When exposed to air, it forms a thin, colorless, tough, oxide film that protects its surface from further oxidation and chemical reaction.
Aluminum ingots (1,500 lb sows) are melted and spray atomized under high pressure into a fine granular powder. Two types of powder can be produced depending upon the atomizing gas that is used to "pick off" the molten aluminum from a nozzle tip. When super heated air is used, conventional round, but irregular, shapes are produced as they oxidize and cool immediately.
Alternatively, when a heated inert gas is used as the atomizing gas, less oxygen is available for aluminum oxidation and, therefore, the molten aluminum particle remains fluid longer allowing surface/interfacial tension forces to produce a spherical particle.
To ensure both proper particle size and distribution for the intended application, the atomized powder is screened (sieved) before final packing. Besides aluminum pigments, other uses of atomized powder include the production of fuels for weapons and rockets, chemical intermediates for deodorants, powder metallurgy that is pressed into aluminum parts, and as fillers for epoxy castings where the aluminum acts as a heat sink assisting in the dissipation of surface heat generated by grinding wheels.
Aluminum Pigment Production
Aluminum pigments are produced almost exclusively using the Hall process which is a wet milling process utilizing mineral spirits. Dry milling is not done due to safety concerns. Typically, mineral spirits and a fatty acid lubricant are added to the ball mills along with the aluminum powder. The slurry concentration of aluminum is only 4%. The mills are rotated at a speed that allows the balls and the aluminum slurry to cascade whereby the impact flattens and breaks the resulting flake. The fatty acid acts as a lubricant to
avoid cold welding of the pigment. The aluminum is milled (2-15 hours) into flakes (cornflake and "silver dollar" like shapes) to a specified fineness and particle size distribution. The milling parameters and the lubricant choice are determined by the intended application of the pigment.
For standard leafing grades, the slurry is pumped into a filter press where most of the solvent is removed. A typical presscake would have 70-80% non volatile. The presscake is added to a mixer where the metal content is adjusted with fresh solvent to a standard combination of 65% aluminum and 35% solvent by weight. During this stage, the final product can be adapted for its subsequent application by the addition of special solvents and/or additives. Products for plastic applications would require a solvent exchange with medical oil or plasticizers (DINP).
Dry aluminum flake products are produced by taking presscake and pulling off the solvent in a vacuum dryer. Some flake products are coated by reacting a polymer onto the surface or can be pasted out with an appropriate solvent.
Leafing or Non-Leafing
Aluminum pigments are classified as either leafing or non-leafing. The type of lubricant utilized in the ball mill determines this property as the pigments surface tension is affected. Stearic acid, which is both hydrophobic and oleophobic, will produce a pigment with high interfacial tension and, thus, make it more difficult for the binder/solvent to wet its surface. Thus, with leafing pigments, when the flake rises to the surface (as a result of convection currents due to solvent evaporation), it is allowed to stay afloat (lack of wetting) forming an overlapping, scale like, dense layer which appears bright and silvery. Akin to a wax coated needle on the surface of water.
Non-leafing pigments are created by the use of oleic acid during the milling operation or by the addition of strongly polar substances or wetting agents to leafing pigments. Non-leafing pigments are completely wetted by the binder and are, thus, dispersed evenly throughout the film. Due to the fact that the pigment orients below the surface of the film, the coatings are more rub fast, abrasion resistant, and can be topcoated. Additionally, combination with colored pigments are possible leading to polychromatic (i.e. "metallic blue") effects.
Aluminum Pigment Properties
Physical Shape
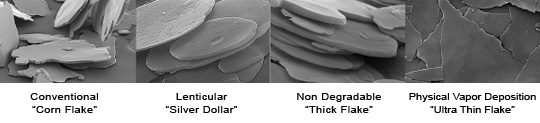
Unlike normal pigments with their granular or spherical shape, aluminum pigments resemble a leaf or a flake. The flake thickness to flake diameter (aspect ratio) can vary from 1:50 to 1:500. The particle shapes vary from irregular flakes (cornflakes) with ragged edges to almost completely round, yet thicker, particles with smooth rounded edges (pancakes or silver dollars). The shape and size of the aluminum pigment determines the hiding power, the color, and degree of sparkle.
Mirror like pigments are obtained in the physical vapor deposition process. A release coating is applied to one side of a polyester or polyolefin carrier film via a coating or printing technique. The coated film is passed through a roller where a very thin aluminum layer (30 – 50 nm) is deposited on the release coat by way of physical vapor deposition.
The metallized film runs through a solvent tank stripper where the release coat is dissolved with either ketones, esters, or alcohols depending on the solubility of the release coat used. The resulting aluminum layer is removed as fragments or coarse flakes. This is subsequently washed and concentrated to a dispersion containing 10 – 20% pigment. The particles are then sized by vigorous stirring or ultrasonic treatment.
Compared to conventional pigments, PVDA pigments allow more specular, or mirror like, reflection than diffuse scattering. These pigments are much thinner (30-50 nm) which enhances their mobility and, thus, allows them to orient parallel to the surface of the substrate much faster. This is beneficial in short drying ink and paint processes. Their relative thinness also contributes to a more uniform flat film appearance where the edges of the flake meet compared to the more obtrusive edges of thicker pigments.
Conventional pigments are exposed to strong mechanical forces during the milling process, which results in uneven flakes with an irregular thickness and a large number of surface defects. PVDA pigments, however, show a homogenous thickness and hardly any surface defects.
Both of these parameters (particle thinness and topography) contribute to higher specular reflection which translates into higher brilliance, flop, and coverage.
Reflectivity
One of the most important properties of aluminum pigments is reflectivity. This is important from both an aesthetic and functional point of view. The reflection of light as well as IR heat and UV is the key property that affects the long term durability of the coating and the substrate itself.
The three primary reasons for coating film degradation are oxygen, moisture and UV light. Coating vehicles either absorb or transmit UV light. Those that absorb will transform the UV light into chemical energy changing the structure of the polymer. This is commonly seen as a loss of gloss, chalking, fading, and yellowing. At the same time, film cracking and delamination can occur which allows oxygen and moisture to penetrate the film and attack both the coating and the substrate that it is protecting.
In the case of leafing pigments, the entire coating will be protected as the pigment congregates at the surface protecting the film below. Leafing pigments allow a higher ability to reflect electromagnetic waves. This makes them ideal for end applications like roof coatings and tank coatings. However, systems which contain highly polar solvents or binders, have high acid values, or contain residual moisture can lead to "de-leafing" of the pigment. Additionally, the fatty acid on the pigment leads to poor intercoat adhesion thus making topcoating difficult. Because leafing pigments are mainly located at the surface of the film, they are not rub fast and have little abrasion resistance.
In the case of non leafing pigments, the action is different. Since the flakes are oriented throughout the film, the resin located above the aluminum is not protected. This layer, in many cases, chalks and is ultimately removed by weather until the aluminum itself is exposed. In this case, the aluminum coating actually experiences an improvement in reflectance, due to chalking action, which exposes the aluminum.
Aluminum also reflects the IR electromagnetic band and, as a result, about 90% of radiated heat is reflected. This is helpful as heat can accelerate the speed of film degradation. Additionally, improved energy conservation is observed as the temperature below an aluminum coated roof is lowered by as much as 10 degrees. In large steel structures (draw bridges, etc), less expansion, due to heat, prevents seizures.
Because of its high heat reflectivity, aluminum exhibits low emmissivity (ability to radiate heat). With 90% reflectivity, only about 7% heat is given off out of the 10% radiant heat that it does pick up. Because of this, aluminum has found markets where a reduction in heat loss from equipment is needed such as furnaces and boilers. This keeps the energy in where it is required and out where a more comfortable environment is needed.
As mentioned earlier, moisture and oxygen are two of the main reasons for coating breakdown. Because of the geometry, orientation, and impervious nature of the aluminum fake, a barrier is created which permits less oxygen and moisture to penetrate the coating’s surface with leafing pigments. In the case of non-leafing, the flakes force moisture and oxygen to snake around them which leads to a much longer path to the substrate. The longer path mechanism for moisture also allows aluminum based coatings to exhibit better sealing and blocking resistance of water stains that telegraph through to subsequent topcoats.
Optics
The electromagnetic wave spectrum includes the following (from large to small) wavelengths: radio, microwave, infra red, visible light, ultraviolet, x-ray, and gamma rays. Each electromagnetic wave has an oscillating electric wave portion (Y-axis) and an oscillating magnetic portion (perpendicular to the electric portion or Z-axis) traveling in a perpendicular direction to both (X-axis) at 186,000 miles/second. The four properties of each wave include its wavelength (crest to crest distance), amplitude (distance from the middle of the wave to its peak), frequency (peaks/second), and directional velocity (miles/second).
The science of light is called optics. Visible light is composed of varying electromagnetic waves (400 – 700 nanometers in wavelength) which is essentially a spectrum of colors. They are visible to humans due to the cones found in our eyeball retinas which are sensitive to red, green, and blue and to which the brain interprets these sensitivities as color. Light waves can be reflected, refracted, transmitted, and absorbed depending on the medium it comes in contact with.
Reflection
Reflection comprises both specular reflection and diffuse scattering. More light is reflected (specular and diffuse) when the change in refractive index (RI) between the two medium interfaces is greater.
Specular reflection is where the angle of refection is equal to the angle of incidence and occurs with very smooth surfaces like mirrors, metallic substrates, and pearlescent pigments. Therefore, perfectly specular surfaces, like mirrors, results in 100% specular reflection.
Diffuse reflection, or scattering, is where the angle of reflection is at all angles and does not equal the angle of incidence. This is true for irregular or rough surfaces like absorption pigments. Perfectly dull surfaces results in 100% diffuse scattering.
Metallic pigments create their effect through both reflection and scattering. They exhibit specular reflection due to its flatness or smoothness, and they exhibit diffuse scattering due to its rough edges and/or defects of its surface.
Incidentally, in scattering, white light emerges unless the particles that light comes in contact with are smaller than the wavelength of light and are uniform in size. In that case, selective scattering occurs which answers the age old questions as to "Why is the sky blue?" and "Why are sunsets red?"
Refraction
Refraction of light occurs when it passes from one medium (for example air with an RI of 1) into another medium (glass, water, mica, TiO2, etc) with a different RI. As a result, both the light speed and direction are altered. Going from a low RI medium to a high RI medium would slow down light’s speed and bend it towards the normal (a line drawn perpendicular to the surface). However, going from a high RI medium to a low RI medium would accelerate light’s speed and bend it away from the normal.
Transmission
Transmission of light occurs with transparent substrates like glass and pearlescent pigments.
Absorption
As for absorption, conventional colored pigments produce the perceived color through the subtractive process of absorption. For example, a blue pigment, illuminated by white light, absorbs most of the visible light wavelengths except those corresponding to blue light (red, orange, and yellow). Likewise, a yellow pigment absorbs most of the wavelengths except those corresponding to yellow light (red, orange, and blue). A combination of the blue and yellow pigments leaves green behind and, thus, we perceive that color when those two pigments are blended.
Optical Properties of Metallic Pigments
The optical properties of metallic pigments include shade, brightness (whiteness), brilliance (sparkle and metallic gloss), tinting strength (hiding power), color saturation, DOI (distinctiveness of image), and flop (the change in brightness in relation to the view angle). These metallic effect properties are determined by particle size, particle size distribution, particle shape (cornflake vs silver dollar), the shape factor (aspect ratio), surface smoothness, pigment orientation in relation to the surface of the substrate, and wetting behavior (leafing vs non-leafing).
With respect to particle size, the visual impression created depends on the ratio between specular reflected and diffuse scattered light. The proportion of specular reflected light increases with the size of the pigment area and the proportion of diffuse scattered light increases with the number of edges scattering the light. The coarser the particle size (and the rounder the shape of the particle) the higher the proportion of specular reflected light and, therefore, the better the brightness, brilliance, color saturation, and flop. The finer the particle size (and the more irregular the particle structure) the higher the proportion of diffuse scattered light and, therefore, the greater the hiding power or coverage. DOI also improves with finer particle size. The higher the DOI, the clearer the refection is of objects with high contrast (buildings, clouds, trees, etc) on painted surfaces.
With respect to pigment orientation, the best optical properties are achieved when the flakes lie parallel to the surface of the film. Improved orientation of the flakes will result in improved brilliance and the metallic effect. Poor orientation leads to "clouding" or to an uneven "salt and pepper" effect. The orientation of flake pigments depends mainly on the formulation and application conditions.
Evaporation of solvent causes the film to shrink and virtually press the aluminum pigments into a horizontal position. The higher the solvent content of the paint, the more pronounced this effect is. Therefore, pigment orientation and, thus, optical properties of low solids paints are considerably better than those of higher solids paints. In higher solids, and thus higher viscosity systems, there is more drag on the flat surface of the pigment during migration within the system forcing them to orient towards the pigment end.
The evaporating solvent creates powerful turbulences within the wet film and if evaporation is too slow it will hinder the orientation of the aluminum pigment through the formation of Bernard cells (clouding). It is helpful, therefore, to use binders which release solvent quickly (i.e. cellulose acetate butyrate) or to include additives which will mollify the "bronzing" effect. There is some positive effect utilizing polyethylene wax dispersions as "distance keepers" and the use of certain surface active agents.
Mechanical Stability
Extremely thin metallic pigments are sensitive to high mechanical shear forces. This may result in deformation and/or fracturing of pigment particles which would adversely affect optical properties. Additionally, any unprotected metal surfaces created due to these shear forces may lead to chemical reaction, gassing, and reduction in product shelf life. Attention, therefore, needs to be given to how these pigments are dispersed or processed by pump systems and circulating lines.
Aluminum pigments are subjected to mechanical shear forces upon the use of metallic paints in areas such as the automotive industry. Pumping systems and the pressure control valves between the constant circulation system, and the spraying device, can damage the pigment. Special aluminum pigments (non-degrading flakes) have been developed for such aggressive circulation lines. The greater thickness of these flakes gives these products higher mechanical stability, but the altered geometry may have an adverse affect on orientation, flop, and color intensity.
Chemical Stability
The chemical properties of aluminum severely limit the choice of binders and solvents. In solventborne systems, acid media could lead to gas formation and graying while alkaline media, or the use of halogen containing products, could also lead to gas formation. Chlorinated hydrocarbons should be avoided as they may lead to HCl formation which would react with finely dispersed pigments. Water should also be avoided with unstabilized pigments.
Aluminum pigments in the presence of water leads to hydrogen gassing. The chemical reaction is as follows:
2 Al + 6 H2O → 2 Al(OH)3 + 3 H2
Two different stabilization procedures can be employed to mitigate gassing. The additive approach utilizes passivating inhibitors (phosphorous-organic compounds) which physically or chemically adsorb onto the pigment surface (phosphorous has a high affinity to aluminum). The "encapsulation" approach utilizes either an organic (chromium based) or inorganic (silica based) coating which coats each pigment particle.
Brass Pigments
Brass pigments (also known as bronze or gold pigments) are alloys of copper and zinc. Unlike aluminum pigments, they are dry milled with stearic acid via the Hametag process.
The range of shades, from pale to rich, is based on varying proportions of copper and zinc used in the alloy. The higher the zinc content, the "richer" the appearance of the pigment to simulate gold color. For improved chemical resistance and color stability at high curing temperatures, these pigments are silica coated.
Zinc Pigments
The production of zinc pigments starts with the atomization of zinc ingots which is subsequently screened and homogenized into zinc granules. These granules can then either be steel ball wet milled (mineral spirits + lubricant) or steel ball dry milled (lubricant only) into the final zinc paste or zinc flake form.
Apart from the cathodic corrosion protection provided by zinc, the flake form has a markedly larger surface area than the spherical zinc dust form. As a result, the higher surface contact between the zinc flake and the steel substrate to be protected results in improved corrosion resistance.
Flake orientation also offers excellent barrier protection, similar to aluminum flake orientation, since longer diffusion paths are encountered to the substrate to be protected. Additionally, the higher binder demand, due to larger surface areas, dictates lower PVCs which in turn leads to favorable application and paint properties.
Upcoming back2basics Issues
In our next issue of back2basics, we will review the world of surfactants — its chemistry, theory, and application in waterborne formulations.
Contact Us
If we can be of any assistance with any of your "effect pigment" requirements, feel free to contact us at 914.273.0300.
|